| |
Project Journal - D10 Restoration |
Handle: |
YTSupport |
|
Project Name: |
D10 Restoration |
|
Tractor: |
AC D10 |
|
Started: |
05:52 11/22/17 |
|
Updated: |
10:34 01/30/19 |
|
|
Expand/Contract all Journal Entries Show newest journal entry on top |
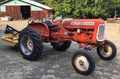 06:48 11/22/17
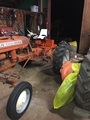 06:48 11/22/17
| 06:48 11/22/17 Initial ProblemsKim bought a D10 and I bought a D12 respectively, to restore. This was not something to undertake immediately, because the first priority was finishing the rebuild of the Yesterday's Tractors D14. The D10 is a Series III and at first glance was an excellent specimen of an original machine, no mods at all, no paint jobs in the past etc. She plans to use it for bush hogging in the spring, and we decided we would hold off on the cosmetic and minor mechanical restoration items until the shop was clear. We simultaneously have the Oliver 1950FWA which needs a lot of work. My shop just isn't big enough for all of these machines at once. While the D10 and D12 await their turn, my son's job is to keep them running and exercised. In my experience with the probably 30 tractors I've had, if you purchase a good tractor and let it sit, it will become junk in short order.
In the course of keeping the D10 running, a problem with the electrical developed, a bad ground that would spark and generally keep the tractor from starting at times. We decided to roll it over to the shop and fix as few things as possible, not really start the restoration but just get the electrical connections cleaned up. As you know, it can be extremely difficult to do "just a little" work on a tractor you are excited about restoring. It's not only excitement that causes this, it's also that each little problem, is usually the tip of an iceberg, and very quickly, things can spiral into a larger project than you have time and space to deal with. I tried very hard to avoid this, but there were a few problems that screamed to be fixed right up front.
The electrical problem was a more serious issue that I initially thought. It did have a bad ground cable so that seemed simple enough. But putting on a new one, really didn't help and we got out the fluke and started checking just how good a ground we were getting from the bolts where the D10 is supposed to be grounded (one of the fender mount bolts). On closer examination, I couldn't find a good ground anywhere on the rear of the tractor. This led to disassembling fenders, mounts, operator platform, pulling the battery out, all cables, and seat. When we removed the battery and seat, we found the problem. The corrosion from the battery had seriously damaged all of these components. It was not obvious that this tractor was rusted until we pulled everything off, but the rot was severe. I didn't want to just create good connections with rotted parts, nor did I think it prudent to put expensive cabling in on junk. So all the components mentioned were sandblasted, the worst corrosion treated with soda, then POR-15, primed and painted in Persian number 2. While this was happening, the fenders, which are extremely expensive to replace, lighting, and mounts were removed and left off. Replacing the rotted sections in the panels will be a body work job of patch panel replacement, restoring the light cans and mounts will involve machining and maybe even some casting. I'm limiting the project by not putting those back on but keeping them in the shop where I can work on them when not working on other projects. We also had new tires for this machine, so it seemed a good time to replace those and one of the rims that was badly cracked. The last thing was that the seat mount and pan were far more damaged that we realized initially. The bushings needed replacement in the seat spring assembly, the bolt that holds the shock in place was bent, and the pan needed sand blasting and painting as the inside was seriously rusted.
Fixing the above problems, was how far we decided to take it this time, then once the tractor was back on the road and not clogging the main entrance to the shop, at leisure we'd fix a few other minor issues that can be done prior to the real restoration later this winter. These were a leaky pan gasket, leaky oil filter mount, gauge replacement (and thus a new wiring harness), filling the steering wheel cracks with epoxy, replacing the inappropriate sediment bowl, and rebuilding the carb since it has a leaky float valve. These can all be done as day jobs so the tractor can be brought from the barn and occupy the shop just for the short time required to do them. Since we have multiple machines to deal with, the D14 restore is taking up one bay of the shop, and the rest of the tractors need to share the other when necessary. I'm also batching together projects like the patch panels for the fenders on this one, with the more serious patch panels required for the D15D restoration (other than the fenders, this tractor is not due for a couple of weeks). That way, the TIG work necessary can all be done in one shot after practicing up. I haven't done sheet metal welding for 17 years, plus I always used MIG, and there will be just one shot to do it right on all four of these fenders, they are getting harder to find in good condition.
For this entry, I'm just going to show the before and after of this interim project, and will make other entries for the individual projects to this point. Then after the first of the year, hopefully we'll be ready to start the full cosmetic restoration and I'll include that here too as separate journal entries. Note, the "After" picture is not really after, this was a mock up before I drilled and installed the new battery box or ran the new cabling. The seat is also not mounted on there because while we are working on it, that beautiful white and black seat, will get dirty from our grimy work coveralls. As this stage completed, we have just the old seat cushion back on it. Also note that in this picture, the new battery box is backward, when I drilled it and installed, it's was oriented appropriately for the Series III.
| | |
|
| 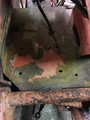 20:18 11/29/17
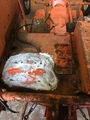 20:18 11/29/17
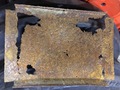 20:18 11/29/17
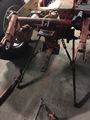 20:18 11/29/17
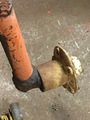 20:18 11/29/17
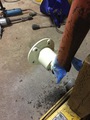 20:18 11/29/17
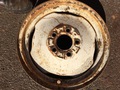 20:18 11/29/17
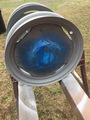 20:18 11/29/17
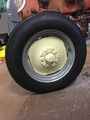 20:18 11/29/17
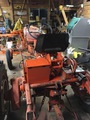 20:18 11/29/17
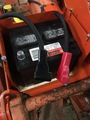 20:18 11/29/17
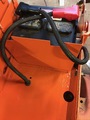 20:18 11/29/17
| 20:18 11/29/17 Restoration BeginsThe D10 is really not supposed to be restored yet. It on the list, but the list is long. Nonetheless, when one day it wouldn't start and the battery connections just threw out fireworks, we had to do something. In a way, that work is the beginning of the restoration.
We decided to tear down just what was necessary to clean up the ground connections, and as we pulled off parts, plus since it was stuck in the shop while we did that, we tried to get as many small issues out of the way now. We pulled off the hitch so we could remove the fender supports. That meant fenders, tool box, operator platform, and what was left of the battery box. After pulling the battery out, and exposing the rotted 1/8 inch steel around the battery box, not to mention the rotted 16 gauge that once was a battery box, we knew we had more work to do.
At this point we decided to replace the cables with the quality wiring we'd purchased from CE Auto Electric (Yesterday's Tractors only sells wiring for a minimal number of tractors, if you are working on an Allis, the place to buy wiring is CE Auto, they have very seriously high quality wire, and you can get it in lengths that match the job, most high quality wire is only purchasable in spools, and unless you are wiring 10 tractors, it's impractical). This meant pulling the side covers and that meant pulling the steering arm first.
After everything was disassembled, we used a baking soda paste on everything that had been damaged by battery acid. It wouldn't do to prime and paint if we didn't stop the reactions. Before that, everything we pulled off had to be heavily wire brushed at a minimum and in some cases, sand blasted. We made good used of the Skat Blast cabinet since there are not parts on the D10, that won't fit in the cabinet.
When it came time to paint, I decided to try POR-15. It is supposed to stop rust dead in it's tracks and I'm hoping it will do that. The downside is that it dries very slick, but it also had a tendency to ball up in spots. By the time we start the real restoration, I should know how effective it is. Those parts that got the POR-15 treatment and the rest of the parts, received primer and Persian #2. It's a bit frustrating to limit oneself to just a part of the tractor. The contrast between the original and newly painted parts is striking, and to my mind, not a nice contrast. Reassembly of the painted and cleaned parts, involved removing the paint from the specific areas where the ground connections needed to be good.
Meanwhile, since the tractor was laid up, we pulled the rims off, replaced the one that had a crack in it, and after sand-blasting and treating the inside of the rims with POR-15, we painted them up, and put the new tires on. That of course meant cleaning and painting the hubs too, which since I didn't pull them, that will be a future job.
Finally we put it all back together with the new wiring. Since we were using very high quality wire, we put the best loom on it I could find, and ran the wires for the future fender lighting that will go on with the restoration. We also used battery, ground and starter connections that were pressed on rather than the screw on type you get at the auto parts store.
When it was all together, the work was worth it. All the grounding problems were gone and it started and ran like a top. Now we can put it back to bed in the barn until we are ready for it.
A lot of parts stayed off it, so I could work on them in my spare time. The rot had progressed to the fenders and tool box, and those will require patch panels. The light cans were damaged and the rare bolts that hold them on stripped, those had to be cut off. We did managed to clean up years of hydraulic oil and dirt sludge, and the tractor will be quite easy to finalize for painting when it's time comes.
I was happy with this turn of events because now I can keep the D10 in line and the second bay of the shop clear for work on the current project, the D14. | | |
|
| 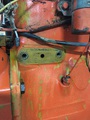 06:45 05/30/18
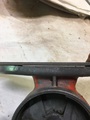 06:45 05/30/18
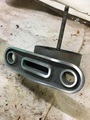 06:45 05/30/18
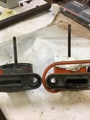 06:45 05/30/18
| 06:45 05/30/18 Oil IssuesThe first order of business getting back to this, was sealing up the oil leaks. It appeared that the rear seal, oil pan gasket and oil filter base were all leaking. The oil filter base was the worst so I cleaned it up, contained the oil coming out of it, then let it sit for a couple of days and no oil came out of the pan or rear seal. It appears that it's just the oil filter base leaking on everything else. I removed it and the tubes connecting it to the pump and oil pressure gauge. Not only had it been installed with nothing but a black silicone (no cork gasket), but it also was warped badly. All cleaned up, it rocked more than 1/16th of an inch when pressed against the surface of the block. The gasket could not take up this slack. I lapped the surface flat removing probably a 1/16 and now the gasket should be able to take up irregularities. It has another issue which I'm not comfortable with. The tube that goes up into the oil filter, is nearly an inch shorter than all the other ones I have laying around. I don't think that was a factory mod but almost looks like someone cut it off, then redrilled the side holes. I'm going to reinstall this one since one additional problem is, new 3/8s holes were drilled in the block to accept this rather than the normal 5/16s. The oil base was also drilled out to match this, so replacing the tube would make more sense if I do anything with it. Right now, reinstalling and getting this sealed is the first order, so I can see if I also need to do pan gasket or rear seal. Since I have a spare base tube of the right length, I will probably replace this short one, I don't think it's right and will limit the oil filters effectiveness. After seeing how badly the oil filter was installed, it might make sense to do the pan just to be sure. It also has a mess of black silicone and also may not have been put together with a gasket. If I'm unable to see one after close examination, I'll pull the pan and put a real gasket on it.
Update: 06/01/18 The leveling on the oil base worked like a charm. Installed and ran for 10 minutes with new oil, parked it for the night with a clean white butcher paper under it. No drips and not even any seepage around any of the gaskets. Going to call that success. I replaced the short tube, because someone had hacked this base up, I had to jb weld it (just a bit), it was way too sloppy in there. Oil pressure is perfect. | | |
|
| 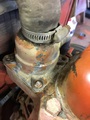 07:37 06/02/18
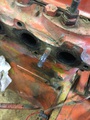 07:37 06/02/18
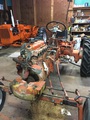 07:37 06/02/18
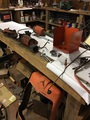 07:37 06/02/18
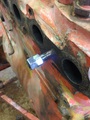 08:15 06/03/18
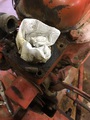 08:15 06/03/18
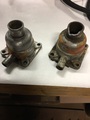 08:15 06/03/18
| 07:37 06/02/18 Manifold and MufflerThe muffler had a large hole in it, and it was an underhood. This dumps exhaust and sparks downward and is too dangerous during the late cutting season. We have a oval up pipe on the way so I removed the muffler in prep. The mounting bolt on the manifold snapped as I expected, and the mount that connected to the thermostat housing also had to come off, meaning the thermostat housing did too, because, that bolt snapped off. Then all but one of the housing bolts snapped off since it had to come off to extract the first. These were all virtually expected. The thermostat housing bolts on the D14 all snapped off too, same with the muffler mount. Also one of the exhaust manifold studs snapped (I figured I was ahead since I lost two off one of these heads last time. My biggest fear in this is that the head will have to come off. The aversion is that this is a very tight well running engine, and removing the head would introduce variables and increase the amount of mechanical work necessary. I'll be rewiring, some machine work on the steering gear, and possibly some hydraulics work, but mostly this was supposed to be a cosmetic restoration at least as far as the engine goes. Another interesting thing that could indicate more mechanical work, is that the front cover of the engine was more caked with grime (dirt and oil) that we might find that the front seal leaks now that we've removed all that dirt. It was an inch thick in some spots and could have been hiding leaks.
Anyway, though no surprises, you always hope you can avoid a day or more of painstaking work extracting broken bolts. So far only one of these requires drilling and that will be the most time consuming one. Still can count on spending most of the day getting these out and cleaned up. My son will work the rest of the disassembly, and I expect to be painting some parts before the weekend is out.
Update: 06/03/18: All the broken studs came out. I spent virtually the entire day on them due to being extremely cautious. I did NOT want to pull the head on this tractor. The Thermostat housing broke pulling it off, the warning is that nothing but hand pressure should be used to break it loose from the broken studs. I don't believe you can remove the thermostat housing bolts without snapping a few off. The bolts "weld" themselves to the pot metal (correction: it's aluminum thanks to someone on the forum who pointed that out, I had no idea but that explains why these casings have such a tendency to bind themselves to the capscrews). I pulled the parts D14's housing and cleaned it up to replace the broken one. I broke it by using a pipe in the upper outlet to get leverage. You can't do this period. Glad I had a second housing. Removal of the studs from the housing outlet, required only small vice grips and I snuck up on them with pressure. Removal of the manifold stud was also a finesse operation. I threaded the stud with a 3/8s die, put two nuts on it so they were locked on, then using an open end on one side, and the vice grips clamped close to the head and out the other side (so it was like having a T-handle, I could put even pressure on both sides and not snap the stud off in the head. It still took a lot of pressure to get it out, but I felt confident I was using balanced pressure. The manifold bolt is still broken off, but I'm taking that to my brother's mill so he can us an end mill on it. I have not had good luck drilling out studs like this since the hole must be perfectly centered. Using an end mill and a solidly built mill, means no mistakes.
We also removed the hitch and drained all the fluids from transmission, hydraulic/pto case, and two-speed transmission. Not looking like this weekend will net any paint work, too much to clean first.
Interesting note on the assembly of the thermostat housing. On the D10, D12, D14, and D15 (G-149 version), Allis Chalmers used an odd size bolt on the right rear bolt of the housing. In my experience, it's always a 5/16s shank with a 7/16s head (rather than a 1/2 inch head as a normal 5/16s bolt would have). I doubt I could even buy one, but there must have been some reason and it's always fascinated me. | | |
|
| 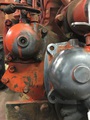 07:34 06/04/18
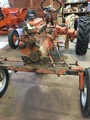 08:45 06/06/18
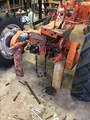 08:45 06/06/18
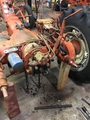 20:25 06/08/18
| 07:34 06/04/18 Governor and more cleanupPulled the rest of the front down and removed the D10 Series III front weight, not the external one, but the internal radiator support. With both weights on the front, this machine has more front weight than the D14. Both weights are massive. Was able to clean more effectively as a result but it's a surprisingly slow process. While cleaning, I found the governor has a hole in the front of it. None of the others I've had have this and someone, glued a plug in it sometime in it's history. Folks on the forums say there is no pressure to speak of in the governor/distributor cases, so I'll glue a new plug on. I knocked this one loose cleaning and when the fan hit it during a test starting, it tore it off. The photo shows a normal cover and this cover. I'll cut a small circle of pot metal and JB Weld into the indentation after cleaning the surface of old glue. Should be able to sand/grind it smooth and it will appear to be stock then.
Plan is currently to remove ops foot rests, rams and swinging drawbar. That should be far enough down to get at everything and clean up the rear. On top, steering wheel, steering gear, dash and tank support are coming off and that will provide cleaning and wiring access, plus I want to work on the internals of the steering gear. It has a strange feeling at the middle tooth, and I think it will require a new gear or maybe a trip to the machine shop. I doubt I'll easily find any replacement parts for it. It's a Ross, but far different than the common B/C/CA steering gears. It appears there is also a stripped bolt held captive in the steering gear case by the throttle linkage. Need to check that out too.
6/6/18: Continued cleanup showed me that this is the dirtiest tractor I've every worked on. Most is gone now, but we've removed pounds of greasy dirt, one inch thick in spots. One other first is that the hydraulic console is designed horribly. That's the square box tilted off the back of the tractor. Removal of this box is not possible without undoing all the hydraulic lines. I don't want to remove them because they are tight, leak free and working perfectly. At this point, it's either going to have some dirt and grime up inside the box, or maybe I'll relent and remove the hydraulic lines. The fender mount can't be removed because it's a large 15/16s head, exposed bottom through the casting and rusted in place. With that hydraulic console in the way, there is no way to break it loose. This will probably be the deciding factor with proceeding to remove all the hydraulics. I don't feel comfortable leaving that rust uncleaned and treated. Another poor engineering decision was the foot platforms. The left side will not come off without dropping the supports underneath, meaning it can't be cleaned well unless we do. So again, we'll probably be disassembling further than I would have preferred. Front end is going to have to come off to separate the roll shift axle spindle sections. Work will have to be done in small chucks, painting some parts with all but clear coat, then reassembling and paint others while repainting the parts already hit. The reason is that so much of it is inaccessible assembled, but the front end should be back on before I hit the main part of the tractor for stability/safety. The same will be true of the rear end. I'll pull the rears and paint the finals but then reassemble before painting the rest of the main frame. In keeping with that, either the roll shift front, or the rear rims and finals will get their first coat by the weekend. The 3M Accuspray system is a godsend for doing piecemeal painting like this, since I can mix a container of primer, Persian #2, and Cream, and keep them sealed for the disjointed work involved. After a few times of reuse, the disposable containers start to lock up as paint hardens in the internal filters, but even then, I dump that paint into a new container, thin it slightly and can continue to use it with opening the main can again.
6/8/18: Clean up continued, and I'm happy to say, I finally got the hydraulic control tower off so I can get all the rust. I also want to clean up the piping. What a mess it is compared to the good old Allis' that had it all internal. What I realized was that though the badly rusted bolts were near impossible to reach on this hydraulic box, they cost a few cents apiece, and cutting them off saves a lot of time. One inch carriage bolts aren't difficult to find, they are stock at every hardware store. I took 3 hours to remove them and the realization hit me so I cut the last on off and was done with it. So now I'm behind quite aways... or I'm just an absurdly optimistic estimator. | | |
|
| 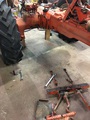 23:59 06/11/18
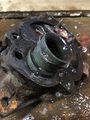 20:53 06/12/18
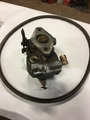 20:53 06/12/18
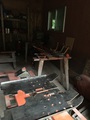 20:53 06/12/18
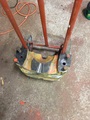 20:53 06/12/18
| 23:59 06/11/18 Ramping up for paintingI know I have to move this tractor fairly quickly if I'm going to take advantage of the good weather and get on to my D15D (or maybe the D12 or D17, not sure yet). We have it all torn down as far as I want to go for a cosmetic restoration, actually further, but it's a very dirty machine. The Idaho soil mixed with grease has made some layers we've never seen before on a tractor. Many parts I've cleaned so far, had very bright original paint underneath, I don't think this tractor was ever cleaned fully in it's lifetime. I have an array of parts, most of the hitch and business end parts, cleaned and placed in the painting stall. As soon as that's full, I'll start primering while my son finishes working on the main frame.
We have to pull the front end off, because the dirt inside the roll-shift front axle tubes is thick. That tube was full and there was only so much I could get out without disassembly. I also have a lot of work to do straightening the radiator shell. Then there is the welding of the fenders and grill, both in poor condition even though it looked perfect before disassembly. I don't know how people manage to ram the front end of every tractor they have. Knock on wood, I don't do that (though I will confess doing it to the front of my last truck with the backhoe loader :-(). The shell is tweaked and really needs straightening. I'm still optimistic that I can get going on the cosmetics soon. I did get the carb in the ultrasonic tonight, I'm hoping it will look like new. I have a rebuild kit for it, but the internals already look very good. Mostly right now, I'm just slugging through the wire brushing of all the parts and one by one, setting them up for paint. I'll get my son to do the dash and steering gear tomorrow. In the process the steering wheel will come off and we'll start jb-welding the plastic back together, it's completely cracked on this tractor, but the JB-Weld worked beautifully to put the D14 steering wheel back together. Having all that off will set us up for the remaining rewiring. The steering gear needs some machine shop work so that's a priority. I reflected on my "Cosmetic Restoration". It seems that no tractor this old in original condition can be "cosmetically restored". You tear into it and too much pops out that needs mechanical work. My impression is that when a tractor has just been used, even if it looks good, it's tired, and it deserves fixing everything you come across. I won't be doing all the seals and engine rebuild on it, but it's still a lot more than cosmetics. You really can't avoid that without blinding yourself to all the little things that are going to break when you start using it. Kim will actually be using this machine for it's intended purpose. That is what we do with tractors, we don't show them, so there is no way to shortcut the process. I guess I'm thinking of it as a cosmetic restoration, just because I'm not rebuilding the engine.
06/12/18: I shot a photo of the venturi direction just because with some of these carbs, it's possible to put it upside down and still get the halves together. Note to self, this is how it goes together. The carb was very dirty but is cleaning up nicely. You can see in the next photo that with just a little wire brushing, it starts to look new. I'll be painting it in orange so I don't need to get the dark spots brushed. The pinesol-water mix I use to clean them, does leave it a little dark. But the halves are very clean and I'll put the rebuild kit in it tomorrow. Lots of other parts are starting to be stacked in the painting area. When that fills up, I'll prime them all. I'll be doing most of the sheet metal separately so I can spend time and care on getting those pieces nicely glossy and a thicker clear than on the cast and heavy steel pieces. The bottom photo is the front inner weight, very heavy. I went to pick it up thinking it was 90 pounds, no way, way over that. Got a lot done for being a bit preoccupied. I bought my D19 and am quite excited about that. Will be months before I get it unless I can arrange a deal on a C6500 GMC Rollback I'm looking at. My trailer won't haul a D19... even close.
06/19/18: Still plugging along cleaning a few parts each night. I have a nearly full paint bay full of parts to prime so I'll break off and paint most of those soon. I'll take them through the Persian Orange #2 coatings before I stop and start the next batch. The next batch will be the main tractor and the large sheet metal pieces which will require a lot of straightening, welding and time consuming work. I did run into a serious glitch with the steering gear. I can't get the steering wheel off without destroying it. The nut was so rusted that it's smaller than the socket that should fit it, by one whole size. It's a sloppy fit too, so if I use the smaller socket, I'm certain it will round off. I was hoping to salvage this steering wheel, so I'm going to try and disassemble the steering gear without removing it. I'm certain the steering gear will need a trip to the machine shop. The manifold I was going to save is not salvageable. I purchased a new one. Slow going at this stage, every thing I removed seemed to cause additional work, but that is the way it usually goes. You can't estimate the time for a restoration accurately, everything requires three or four times the labor you would expect if the parts were all new. | | |
|
| 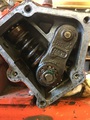 13:58 06/23/18
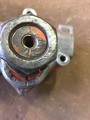 13:58 06/23/18
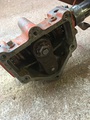 13:58 06/23/18
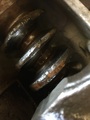 13:58 06/23/18
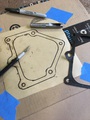 13:58 06/23/18
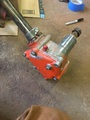 13:58 06/23/18
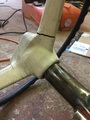 13:58 06/23/18
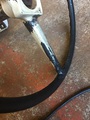 20:37 06/25/18
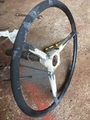 20:37 06/25/18
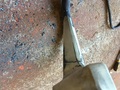 21:45 06/26/18
| 13:58 06/23/18 Steering gearThe steering gear felt nasty. It had a spot at center where it just clicked and felt ever so slightly like there was a grind at that point. I pulled it off even though I couldn't remove the steering wheel (without destroying it), and opened up the case. It appears it had never been adjusted. This was almost understandable because the throttle is mounted such that it can't be adjusted. Not sure how that happened. The end result was that the worm was fairly chewed up and I had to remove a lot of steel out of the bottom of the case. I rinsed it out, blew it out, made a gasket, then lined it up so it was at precise mid-point (note how the shaft has punches to help with that when you don't have the back of the case off), put it back together and adjusted it per the manual, a slight drag at the mid-point is their instruction. Cleaned it up and put it all back together and will hope for the best. Tightened up, I'm hoping the damage to the worm gear won't be a problem.
I have to JB-Weld the steering wheel cracks today. That's worked out well for me in past restorations. After that dries and I file and sand it to the appropriate profile, it will go in the painting room and wait for the batch to be done. The photo shows the worst crack, but it appears there are at least 10 to fill.
The JB-Weld has dried and my son spent the day shaping with a couple of files (flat and a round file). It's coming out beautifully. With paint, it won't be obvious that it had any cracks in it. It's always dicey whether JB-Weld is up to the task of holding the plastic together, but it's worked fine for me thus far on every tractor I've done. It beats paying for a new steering wheel, though it could be the labor doesn't justify the savings, I still would choose to use the original part if possible.
Update, the new picture shows the same crack that looked so bad. The steering wheel is shaping up fine. With the JB-Weld jammed down in there, it should hold fine and with paint, none of the cracks will show. Son is doing a great job on it. | | |
|
| 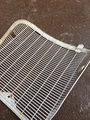 20:47 06/25/18
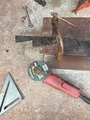 20:47 06/25/18
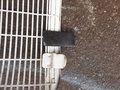 20:47 06/25/18
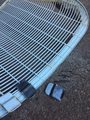 21:44 06/26/18
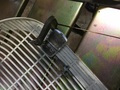 20:44 06/28/18
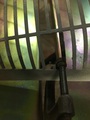 20:44 06/28/18
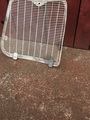 20:44 06/28/18
| 20:47 06/25/18 Grill RepairThe grill was damaged at some point in this tractors life. Two of the clips that hold it to the radiator shroud are gone and with them, the small pieces of grill itself. I'm going to make new pieces for the clips and small slices to weld in to replace the missing "rungs" of the grill. My plan is to try and use very low amperage TIG and take my time. It will go down to 5 amps, but the starting amperage is quiet a bit higher. I'm going to try to put a heavy piece of steel over the small parts to let the start occur, then transition onto the real material I want to weld. The clips look to be about 16 gauge sheet metal and that's what I'll be using to create the missing chunks. This is probably something better left to an expert, but I don't have much choice that to do it myself. I'll practice with several thin strips of 16 gauge first and then do the real parts.
Update, new picture shows the new clamps and 3 small slices of sheet steel cut and bent to match the spots where the grill sections were ripped out. Now the trick will be welding them in so they will actually hold. I'm concerned about that. The welding should be easy, but the clamps never had much to hold onto and my replacements will be the same way. Poor design. I'll sandblast the grill tomorrow and if my test welds work, I'll try doing the real thing.
Update, today I welded the grill. It took several hours just doing the layup. The good news is that TIG welding is nothing short of amazing. I ran at 25 amps using a 1/16th inch tungsten. With such low amperage, you really have time to build a pool on small pieces like these without any heat that could produce warpage. The bad news is that I should have more TIG time under my belt before trying something like this. It's not perfect. There are a lot of blobs in places that will be very difficult to grind out smooth, though they are hidden by being on the back side of the grill. It's all in one piece now and what was a botched up grill, looks complete. Tomorrow will be the fenders and I expect that to go very well but time consuming. I'm going to fill what I can with silicon bronze and then weld a patch panel in at one spot that will show. Even though todays work was not perfect, it was good enough that I feel accomplished. | | |
|
| 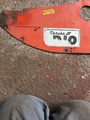 21:19 06/27/18
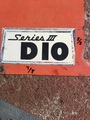 21:19 06/27/18
| 21:19 06/27/18 Decal PlacementHere is the Decal Placement from an original D10 Series III. Not that AC did it the same all the time, but this is how I'll make sure I remember where they were on this tractor.
All the sandblasting and cleaning is done. Tomorrow we weld and clean the rest of the main frame itself. Then it's time to prepare the shop for paint and paint everything. Things are happening pretty quickly. None too soon, I'm getting excited about the either starting the rebuild of the D17D or the D15D. Both the diesels really excite me. That's not to say that this project isn't also challenging. Doing the welding on the grill and fenders is a going to be tough. Especially the grill. | | |
|
| 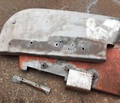 20:03 06/29/18
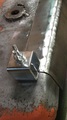 21:52 06/30/18
| 20:03 06/29/18 Fender RepairI mentioned in the grill section that I was going to fill what I could on the holes in the D10 Series III fenders. On one fender, I was able to easily fill in the holes with steel rod. The other was clearly hopeless. There wasn't enough steel left around the rust holes to get a bite, the holes just enlarged even at very low amperage. I decided the patch panels were necessary. Since the the D10 is Kim's tractor, I didn't want to practice on her fenders, so I took my D15D fenders and decided to practice by doing those first. TIG is different and I wanted to be overly cautious, I can't return to wire feeding or stick for this job (too many years away from welding). I spent today cleaning up one of my D15 fenders, making a couple of patch panels, removing the old stock and tomorrow I'll weld them in. I chose the easier of the two D15 fenders as a starter. In the photo, the fender on top is the D10 and under it is the D15, with the rotted section mostly removed, plus half of it's new patch panel is formed and ready. I just have size everything up and start welding. I'll cover that on my D15D restoration project journal. If it goes quickly, since it's Saturday tomorrow, maybe I will get to the D10 fender. The welding is extremely slow, even at 25 amps. I could hear the popping and feared warpage when I welded the two patch panel sections together (necessary because I have no sheet metal other than smaller sections. In fact, I'm cutting down Farmall Cub tool boxes that were partially completed from the last production run I did in the 90s. We used to sell the Cub tool boxes on the site and lots of other folks started to make them in quantity, so I stopped fabricating tractor parts for sale.
Update: I have to say I'm frustrated. You can see the condition of the patch panel, a good fit and I thought I cleaned it well. This is my D15D test before attempting the patch on the D10 fender. The pitting from rust was fairly bad but I had shiny metal after prep. I could not get the fender metal to pool at all. I don't know at this point whether to go up in amperage or not. At 25 amps, I could still burn through the new sheet metal before getting any response from the fender sheet metal. I guess I'll try 30 amps tomorrow, maybe even 35. It's a shame to get the panel fitted so well, then not be able to weld it.
Update:07/03/18 It turned out, the higher amperage was what was needed. I ended up at about 27 amps and then it welded just fine. Unfortunately, I realized after doing the D15 fender, that the rot was just too much in the D10 fender. You can see in the first picture. There is not enough steel to put a patch panel in unless I cut a 20x7 panel, then that would require drilling out the braces. Since this rot won't show, I'm considering just welding panels on the inside of heavy steal, treating the rust and then filling the visual parts in. My D14 has panels like that, and they will last a 100 years, unlike ACs bare sheet metal panels. I'm happy to have gotten so much practice with the TIG though. It's a wonderful welding experience. | | |
|
| 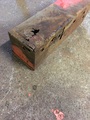 22:11 07/03/18
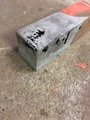 22:11 07/03/18
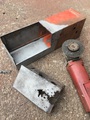 07:01 07/05/18
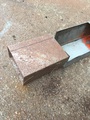 07:01 07/05/18
 07:01 07/05/18
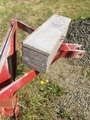 20:44 07/05/18
| 22:11 07/03/18 ToolboxKim wanted to save the tool box. It's pretty far gone. I sandblasted the areas that need replacement so I could see how bad it really was. It's BAD. I'm going to try to patch in though. The most difficult part is drilling square holes. I've seen a video on that before so I'll try to find that again. This should be a real challenge, the metal is very thin on these things. Fortunately, I have two shot tool boxes that I can get the panels out of.
Update from July 4th. I tore into the shot tool box and cut all the rust away. I sacrificed another partially finished Farmall Cub toolbox from 20 years ago as the donor for the sheet metal. The fit up was poor because of the gap left on the back side. Big mistake because bridging that gap with TIG is a nightmare. Ideally, I should be able to set it on an aluminum plate, lay a rod between them and melt it together, then come back through with another pass to make it look nice. Easier said than done though. Going to try that today.
Happy to say the tool box is done. I used an overlap on the end just because it was soooo much easier to weld. It will barely be seen and where I did the bottom and rear welds, they look horrible but they are strong. Note I don't show those in the picture. When you open the box you see the blobby welds but I'll put a piece of 1/4 plywood in the bottom, no one wants metal things vibrating in the tool box anyway. If I could find some rubber sheet, I'd line the entire thing with it. But the tool box is saved and Kim will be happy with it being the original rather than an aftermarket.
Also got the rest of the main frame cleaned up. I just have to find a couple more jack stands, pull off all four wheels and then I'll start the primer. Might be done before August. | | |
|
| 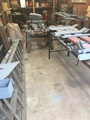 07:06 07/10/18
 07:06 07/10/18
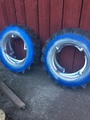 21:46 07/14/18
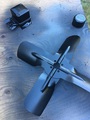 21:46 07/14/18
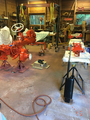 21:46 07/14/18
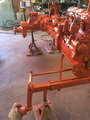 21:46 07/14/18
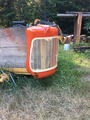 21:46 07/14/18
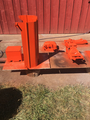 21:46 07/14/18
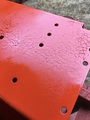 19:42 07/20/18
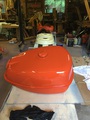 19:42 07/20/18
| 07:06 07/10/18 PaintingYesterday, all the clean-up was finally complete so the painting began. Just primer right now, so virtually everything had to be shot at one time. It took three pots of thinned primer. I let it dry overnight and will flip the parts that require two sided shooting. I find that even though primer dries the fastest and I thin it heavily, if I flip a given part without giving it 24 hours, the new paint will scuff when set against something. Tractor paint, formulated for brushing has to be really thinned and allowed to thoroughly dry before moving to the next step, it's not like auto paint. If you move too fast, it will come right off unless you are brushing and using it straight, but then it takes longer to dry.
Slugging through the painting. The last few days have been doing different colors, hi-temp black, low gloss black, Persian orange #2, Cream and Aluminum. Down to the point where I just have another gallon or so to put on the main tractor and a second coat on a few other parts. I'll be doing three coats on most of it, because I found that in the right light, with two, I get some spots that aren't a nice solid color. That will also let me sand the imperfections without burning through. Then the clear coat should look great. I'll put the decals under the clear again, the edge lines don't disappear as I'd hoped on my last restoration, but they should last much longer. Shuffling things in and out to keep overspray off some parts is quite a physical job, especially the two front weights, both are over 100 pounds. As always with my set up, I have 3 bays full of parts and still have to shoot some parts out in front of the shop. The stuff dries really fast in the sun so I like that, but bug damage causes a lot of rework. I've wracked my brain to think of what I'd need for a tent structure or something to have a clean positive pressure painting area, but the fact is, it would have to be too big anyway for such a special purpose structure.
With the tractor paint, you need to thin it well to get a good dry time. I am doing it as follows, 20% on Creme and Persian Orange #2, none on Aluminum, and 25% on the black. This Tisco Black is amazing. It's the best color I've seen yet for approximating factory generator, voltage regulator, and starter colors. It has such a nice semi-gloss, that I'm not going to clear coat over it. It would be perfect for the muffler (the semi-gloss black oval style) but I have to get the heat rating on it. If it's 600 or better, I'll use it, otherwise I'll pick up VHT gloss black header paint which is rated at 1700, going to check on that today. We don't have it in the catalog, but we can sell it.
I made a serious mistake in masking the rear tires. I masked out only 6 or 7 inches thinking I could just be cautious. I still got overspray on the ribs and had to spend 2 or 3 hours with brake fluid cleaning it off. I had the pressure up higher than it should be for the very thin aluminum paint (it could go as low as 15 PSI), and it was putting out way more overspray than I realized. On the plus side, the tires, which are brand new, actually look better than brand new where I cleaned them, so I'll finish that job after the clear coat and tape removal. My advice is buy a couple of rolls of blue tape and mask way out. On the last restoration, I used paper and that was such a hassle, I just started wasting the blue tape. But that is a fast and durable way to do it. The paper tore as I moved the tires around. But if you use tape, don't be stingy, the time loss in clean up was too much. It's a personal irritant to see paint on the tires of a restored tractor, but removing the tires isn't necessarily a good idea as it may destroy an antique's rims.
I'll try to get photos tonight.
Update: I'm very happy with how things are coming. This will be a working tractor, but I would not be ashamed to show it. The paint is coming out well. I'm really pleased with the TISCO tractor paint too. At the thinning level I'm using, it flows on beautifully and I got 3 runs I could find, none in a place where they matter. I used VHT Caliper Black on the muffler and the appearance is perfect for the original level of gloss. It's good for 900 Fht and that should be fine for the muffler. TISCOs Non-glare black looks perfect too, but they only guarantee it to engine temps, and the bottom of the muffler will be 900. So I have the non-glare black on key engine components and the VHT on the muffler. I also used the 1700 Fht flat black for the top half of the manifold. Anything less would rust too soon for my taste. We need a product for that. We have high-temp but it's not quite as high as the VHT. The problem is cost, the VHT is very expensive. I'm figuring, by next week, the clear coat can start going on. Interesting that it required 4 different gloss levels of black to do this job right.
I ran into one problem that concerns me, there is a small rust pinhole on the tank. It's not functional issue, because the tank is completely sealed, it's cosmetic. That pinhole could grow. It wasn't evident to me because the tank was primed in brown since we got it. The University (of Idaho) that had this tractor sealed the tank and it appears this is why. Had I known that rust was at the surface, I would have sealed that spot from the outside with tank sealer. Now it's painted and of course the rust dot won't take paint. It didn't show up until I started the base color coats. I was being cautious with this tank just because I saw the sealer and primer, I didn't take the top to bare metal and I should have. It requires a magnifying glass to see it, but I know it's there and it's bugging me. What is amazing is, that is the only serious problem I've run into with this paint job. That's pretty good in my experience. I'll correct it as it evolves.
The only other thing is that I sanded the gloss black on the seat and smoothed it out nicely, then put one final coat of gloss over that. It really did the trick to sand with the 2000 grit paper. This coat looks excellent and will be ready for a clear coat.
We have one additional paint problem left. The tank badges are complex. How we repaint the letters of the Allis Chalmers logo, I don't know. Kim has talked about using plastic stencils we make, and that sounds good, but will be very difficult. One positive is if we cut them out individually, they'd be reusable on my D12, D15, and D17, all need the badges refurbished. I'll show a photo of them tomorrow. We could buy new ones and save a lot of money in time, but it would violate Kim's idea of reusing everything possible off the original tractor. I like that idea too even though it's not always efficient use of time. We don't restore tractors to be an efficient use of time. If we go that route, generally my plan is to use walnut shells to blast the batches, as you would to get beautiful cases on shells for reloading, then mask and paint the creme, finally paint non-glare black within stencils for the letters. That's nine total letters that have to be stenciled. Doable.
Tomorrow I'll do more assembly of parts I want to clear coat after they are on the tractor. Particularly, the hitch parts should be done this way but I'm also thinking of doing the hydraulic control panel as an assembly. I already am doing much better than AC did, they shot the tractor originally with the floorboards, battery box assembled, it was all yellow primer under there, no AC #2 orange at all. I can't fault them too much, their paint job lasted 58 years for the most part.
I'll close this part after a couple of shots of clear coat, and that won't be for a few days. Crucial with TISCO tractor paint is to let if dry as completely as possible before shooting the clear coat. As I said in my D14 restoration (and proved much to my chagrin), poly based paint is NOT to be shot quickly. It's not like car paint and it's cross linking is so severe, that the clear coat will lift the base coat right down to the primer if you hurry. Contrary to what the experts say, it will link fine after several days, and it actually works better the longer you give it. I'm going to take a break and work on my sawmill, cut some pastures, clean out my storage building where more tractors are going to go, generally wait and give this tractor drying time.
Another note to add: Ignore the wing nut in P2 orange, that was just on there during the painting to protect the threads on the grill holding stud. I have new chrome wing nuts and washer for that (and the battery box). It's not original as that should be in creme, but I like the chrome.
Update 0717/18: All is going well, a few side steps but I did start some clearcoating today. After frustration trying to use it uncut, I did a 20% cut with paint thinner. I should have used lacquer thinner. It really worked well the first time but failed the second and globbed up the clear. This is Tisco Clear coat and is not warranteed if you cut it, but frankly, it is worth it because you can't get a good non-blotchy finish if you don't. Cut 20% it flowed well through my gun and became a joy to paint. Tomorrow I'll do the first coat on the mainframe of the tractor and second on the parts I painted today. I was painting in almost 80 degree weather. I know that's wrong, but it dries so quickly and well that I like it. Besides, I can't wait for cooler weather, have to finish this machine.
Update 07/18/18: Not so well now. The temperature dropped to about 60 and the clear coat was like molasses. I had run it uncut for a pot and it worked well when the temperature was very high, so did it again today and had to crank the pressure, and just generally, it went on horribly. I ended up with runs as a result (coupled with my poor eyesight, I was not seeing it go on well enough inside). So I have some orange peel areas and runs in the hood. The orange peel will be no problem, it will disappear in the next clear coat, but the runs will take drying and sanding off. I also had to reshoot color coat on the fenders and the hydraulic platform. It is just the way it worked, missed spots on the fender edges, and a bug worked it's way into the platform, when I tried to get him out, I actually scratched the base coat. This paint job has been a tremendous amount of work. I have at least 8 hours into painting right now, maybe more. It'll all work out just because of sand paper and polish, but the more I have to do that, the longer the job will be. It was unfortunate because I was liking the job on the hood. It's always a drag when you like the finish but go for one more coat just to thicken it up, then it comes out poorly. It's deflating. I just have to remember, never paint thick coats of anything, always cut.
Update 07/19/18: I finalized the painting today except for one really dumb problem. To paint with cut clear coat designed for Alkyd paints, you have to wait 48 hours or more. I had redone the hydraulic cover and it looks excellent. I forgot and clear coated it with the other final parts. It immediately lifted the base coat and krinkled it all. That is the second to the last photo. I'll be grinding it all off in the morning, primering it, then hitting it with base coat again. Very unfortunate because that just happens to be the most critical part to start with in putting it back together. I'll be able to assemble somethings and even rewire it this week, but most of the rear end will need till about Friday to assemble. The final picture shows how good everything else came out. The runs are handled and with a nice lacquer thinner 20% cut, the clear coat flowed perfectly. That is the only way to really cut the poly clear coat, but you definitely have to wait the 48 hours before painting a base coated surface. Ignore everything you've read about painting when you use tractor paint. It doesn't work the same way. Sure looks good though.
Time to start reassembling! | | |
|
| 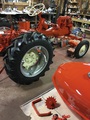 23:15 07/21/18
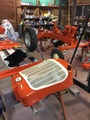 23:15 07/21/18
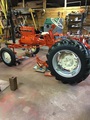 23:15 07/21/18
| 23:15 07/21/18 Painting issues resolvedI managed to correct the problems I ran into at the last of the painting section. The Hydraulic cover is sanded and repainted, now waiting for the countdown to clear coat. Probably Tuesday just to be safe. I started reassembling the tractor and though I did many small parts today, the priority was to get the wheels on and get it off jacks. I won't work seriously on it while it's on jacks, just too dangerous. Put the wheels together and installed them, then brought it down. Did many knobs, hitch parts, and even started doing the generator and voltage regulator mounts. I'm using the internal and external tooth washers to ensure grounds, and testing each connection where a ground is required so there won't be any surprises during the re-wire. A good days work. Need my son here for some of the stuff. It's tough holding some assemblies up, e.g., the brake and clutch platform and bolting it on by yourself.
Update: Unbelievable but I jumped the gun on the hydraulic cover again and once again did it's clear coat wrinkled the base coat again. That's 4 times that piece has had to be resanded and painted. It's waiting again and I'm giving it five days drying time before I do the clear coat. It's slowing me down since it's critical to get on before I can assemble the battery box and finish wiring the rear end. | | |
|
| 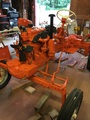 21:35 07/23/18
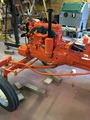 21:35 07/23/18
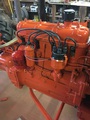 22:50 07/28/18
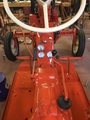 22:50 07/28/18
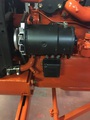 22:50 07/28/18
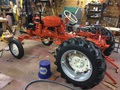 22:12 07/29/18
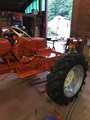 07:23 08/01/18
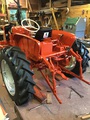 10:21 08/04/18
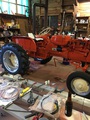 10:21 08/04/18
| 21:35 07/23/18 ReassemblyStarting the reassembly. Put the starter, carb, floor pans, brakes, clutch, air box, front weight and a few pieces on the rear end. The generator mounts and the rear fender mounts were the most important because all needed cleaning so no paint would impact the grounds, plus I used many external tooth lock washers in key places to also aid in good grounds. I also started to install the muffler and discovered the new manifold and new muffler had a horrible fit. I checked with our sales manager and he's never had a complaint. It's a Stanley and shouldn't be that bad, it's nearly a quarter inch off in the plate that bolts to the manifold, it is welded flush with the bottom of the muffler and I think it's supposed to be welded to the OD of the muffler body. I don't want to wait for another so I'll modify the mount bracket to fit. Not difficult but it's disconcerting to have a supplier provide an ill-fitting part because the possibility is there a customer might get one. We'll have to figure that out with them. I'm taking detailed measurements so I can show them the problem.
I got the wiring and gauges done. It's topped up on fluids. No leaks of antifreeze and that's great considering how much trouble I had with that last restore. The wiring still is waiting on the hydraulic cover to wire the lights since the fenders and battery box can't go on until the hydraulic cover goes on. I'm a few days out for finishing this as a result. The Electronic Ignition is done though. Maybe I'll get to the manifold muffler issue tomorrow.
Update: Tanks on, gas lines and brake linkage. Tomorrow is the day to re-clear coat. I'm going to hit the fenders again and the tool box but the most important thing is the hydraulic cover, that's holding everything up. Doing the other pieces again will give a great base to let me level and sand, then polish. Especially with the fenders, it looks so nice when they are perfect.
Update: The hydraulic cover and right fender are on finally. As expected, this was the most difficult job as of yet, getting that cover back in place and all the hitch components connected. One of the negatives was that that fender is painted horribly. I did the work for it's second coat in a dimly lit room, used a highly thinned clear coat (lacquer thinner) and then placed it upright very soon after painting. Apparently I hit the mid section of it too heavy and that thinned clear, ran like the dickens. Since it's installed, I'll be masking off the entire tractor, sanding it and hitting with another coat of clear. It's that bad and I can't avoid doing it. Easily the worst runs I've had on any tractor paint job ever. I now realize I'd run the thinning far beyond what I should have for that pot. I didn't notice it on other pieces, because they dried lying flat.
Update: Battery box, front weight, side panels, other fender, right platform and even a few decals done yesterday. It's ready to start and run it a bit. Wiring is checking out well so far, so running it is the only way I can test out the charging system (along with the new ignition of course). Putting the seat on was a challenge. It's a brand new seat from one of our suppliers and though really a nicely made seat. Some of the mounting holes were drilled off at least for this seat frame. Kim was very against modifying the stock seat frame to match the aftermarket seat, so the issue became one of seeing how it could be mounted as is. We had to tweak it a bit but got it on. Just like withe the muffler, it's going to take some discussions to determine who the manufacturer is and how we can guarantee that a customer doesn't run into this. One of the problems in this business is you don't hear back from customers because like myself, they tolerate a fit issue and work around it. But that is not ideal. It's like we need a questionnaire to go to each buyer asking if the fit was correct and if not, what were the problems. With a customer base of self-sufficient DIY oriented people, sometimes the feedback isn't there unless you use the part yourself. I could be done this weekend but for needing the paint to cure so I can correct, buff, polish and touch up. | | |
|
| 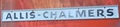 07:24 08/09/18
 07:24 08/09/18
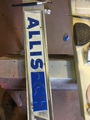 07:24 08/09/18
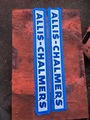 07:24 08/09/18
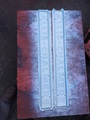 07:24 08/09/18
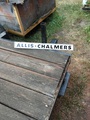 07:24 08/09/18
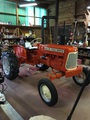 07:24 08/09/18
| 07:24 08/09/18 Hood side badgesI found the hood side badges to be very difficult. I sanded the aluminum rims of the badges, then masked them and the raised lettering with blue tape. To allow the cream background to be painted, I cut around the letters with an exacto knife. This worked but the knife cuts the aluminum badly and you have to be very cautious to not assume you can just cut anywhere. I left it scarred as a result of not being careful. I painted the cream and was going to cut out the tops of the letters so I could pad paint the black tops. This did far too much damage to the letters so I stopped and removed all the masking tape. I bought a paint stik and did a test with it, painting the lettering on my D12s side badge, then clear coating it. The clear coat did loosen the paint stik paint, but didn't lift it. Though I was displeased with the crispness of painting the black letter tops freehand with the stick, I saw no other choice. It looks bad up close, from a few feet back you can't tell. The only other option would have been to buy replacements. This was not an acceptable option on this model, because the font is different on the later side badges. They updated the font by 1964 and thus the replacements would not be right for a D10 Series III.
All that is left to do is the fender lights and the tractor is ready to fire up and use. | | |
|
| 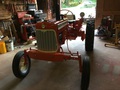 15:35 08/14/18
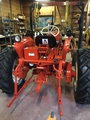 15:35 08/14/18
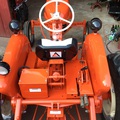 15:35 08/14/18
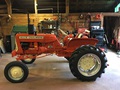 15:35 08/14/18
| 15:35 08/14/18 Calling it DoneWe finished up and fired her up. I had some issues with the black caliper paint on the muffler, it immediately boiled off. I redid it in much higher temp flat black. Also had a minor issue with the valve weeping on the new sediment bowl but aside from that, it's all looking good. We'll be field testing it with the bush hog today.
Calling a tractor done has it's magic to make you a liar, the remotes were leaking and the valve ball seats are just too shot to fix. It was going to run over 60 dollars to replace them and they will never be used (or rather, if they were, finding remote valves that fit a presently undefined application, is not possible). I found caps and am installing them. The weeping on the sediment bowl was from too much binding. I took the sediment bowl off and used the internals from it, with a body from the D14s old one. This should work. Sediment bowls have offset bodies, where that offset ends up makes all the difference in the world. This tractor could not use the type where the valve runs perpendicular to the tractor, it must use the kind that runs parallel (meaning the valve faces the rear of the tractor. That type is identical to the D14 sediment bowl except that it is installed rotated 90 degrees to CCW (when looking down on it). I had seepage around the governor bushing too, it's enough that it troubles me, but it's a large job to fix it. The dirt had masked this problem being inches thick in the front of the tractor. It's not powered out by pressure, so I wasn't aware of this leak. My D14 had this problem and someone had put a wire on it to hold it down, they seem to seep when they climb while the governor is in use, I'll test that with a cable tie. The actual fix though, is to pull it off and find another good governor housing. This means removal of the front weight, shroud, radiator, and fan to do it easily though might be able to snake it out without. But, if I don't find another better housing, it wouldn't be useful to tear it down, I have two extra housings, but one has the same problem, the other I'm not sure about but it feels sloppy too. | | |
|
|  | 10:34 01/30/19 After-restoration mistakeWe had a particularly wet year and the barn was often soaked inside. I had the tractors nestled away for the winter and the didn't block the clutch pedal down on the D10. As a result, this pretty little tractor is now got a stuck clutch which hopefully I'll get apart with some penetrating fluid and then putting a load on it. But it's just something to remember to avoid when you store your tractors. In the case of this on, it's easy to put a wood block in after pushing down the clutch to ensure the clutch disk has no pressure on it. There is always a possibility I'll have to split it to get the disk off the flywheel, and maybe even put a new one in. | | |
|
| |
|
| Return to Journal list |
|
What are Project Journals?
Project Journals are a place where YT Community members can document their tractor and farm projects. Each journal created, can have many photos and accompanying text entries. You can also enable comments to allow other members of the YT Community to comment on your journal. If you do enable comments, it is up to you to moderate what people enter in your journal according to the site policy of Yesterdays Tractors. Journals may also be used as photo posting area, to post your photos of your farm, tractors and related photo topics. If you would like to create a journal, just be sure you are logged in to the Classic View of the forums, and a link will appear to do so when you next come to this page. . |
Home
| Forums
Today's Featured Article -
Restoration Story: Field Marshall Series 1 - by Anthony West. I had been restoring tractors for several years, and over that time had aquired a varied collection of machines of all ilk. I had started on Fordsons both standard and major, and from there progressed as my skills and knowledge increased. It had always been my ambition to own one of the rare types of tractor. The sort of machine that was eagerly talked about at meetings and gloated over lovingly at shows. One such machine was Field Marshall, I had heard many men talk of this machine with a p
... [Read Article]
Latest Ad:
1997 cub cadet 7275 compact utility tractor 4wd hydro trans cracked block 3500
[More Ads]
Copyright © 1997-2024 Yesterday's Tractor Co. All Rights Reserved. Reproduction of any part of this website, including design and content, without written permission is strictly prohibited. Trade Marks and Trade Names contained and used in this Website are those of others, and are used in this Website in a descriptive sense to refer to the products of others. Use of this Web site constitutes acceptance of our User Agreement and Privacy Policy TRADEMARK DISCLAIMER: Tradenames and Trademarks referred to within Yesterday's Tractor Co. products and within the Yesterday's Tractor Co. websites are the property of their respective trademark holders. None of these trademark holders are affiliated with Yesterday's Tractor Co., our products, or our website nor are we sponsored by them. John Deere and its logos are the registered trademarks of the John Deere Corporation. Agco, Agco Allis, White, Massey Ferguson and their logos are the registered trademarks of AGCO Corporation. Case, Case-IH, Farmall, International Harvester, New Holland and their logos are registered trademarks of CNH Global N.V. Yesterday's Tractors - Antique Tractor HeadquartersWebsite Accessibility Policy |
|